Are you facing the challenge of making complex optical lenses with consistent quality through THY Precision Injection Molding Optical Lenses? At THY Precision, we’ve got it down to a science. We deliver reliable, high-quality results for large-scale optical lens production. Let’s dive into the Injection Molding Optical Lenses process step by step to make your production smooth and dependable.
Key Takeaways
- Learn the essential steps in the Injection Molding Optical Lenses process step by step for top-notch optical lens production.
- See how mold design and tooling help get consistent, repeatable results.
- Understand why quality control and monitoring are key in the Injection Molding Optical Lenses process step by step.
- Discover the challenges and best practices for large-scale plastic Injection Molding Optical Lenses of complex optical lenses.
- Explore the latest trends and technologies in injection moulding process step by step for optical lens manufacturing.
Introducing Injection Molding Optical Lenses
At THY Precision, we know how vital the injection moulding process is for making lots of optical lenses. This process has many steps that work together. They make sure we can make high-quality parts quickly and at a good price.
Advantages of Injection Molding Optical Lenses
The injection moulding process has many benefits for making things like optical lenses. These benefits include:
- Rapid production of identical parts, enabling high-volume output
- Exceptional precision and repeatability, ensuring consistent quality
- Cost-effective manufacturing, thanks to the automated nature of the process
- Ability to create intricate, detailed designs with tight tolerances
THY Precision is great at the injection moulding process. We make sure our optical lenses are always top-notch. This process lets us make lots of parts that are the same and do it well and without spending too much.
Step | Description |
---|---|
Clamping the Mold | The first step is to clamp the mold together tightly. This makes sure it can handle the pressure when the plastic is injected. |
Melting and Injecting the Plastic | Then, the plastic gets heated and melted. It’s pushed into the mold under a lot of pressure, filling it with the right shape. |
Cooling and Solidifying | After that, the plastic cools down and hardens in the mold. It takes the exact shape of the mold. |
Ejecting the Finished Part | Finally, the part comes out of the mold. This ends the injection moulding process and gets the part ready for more work or putting it together. |
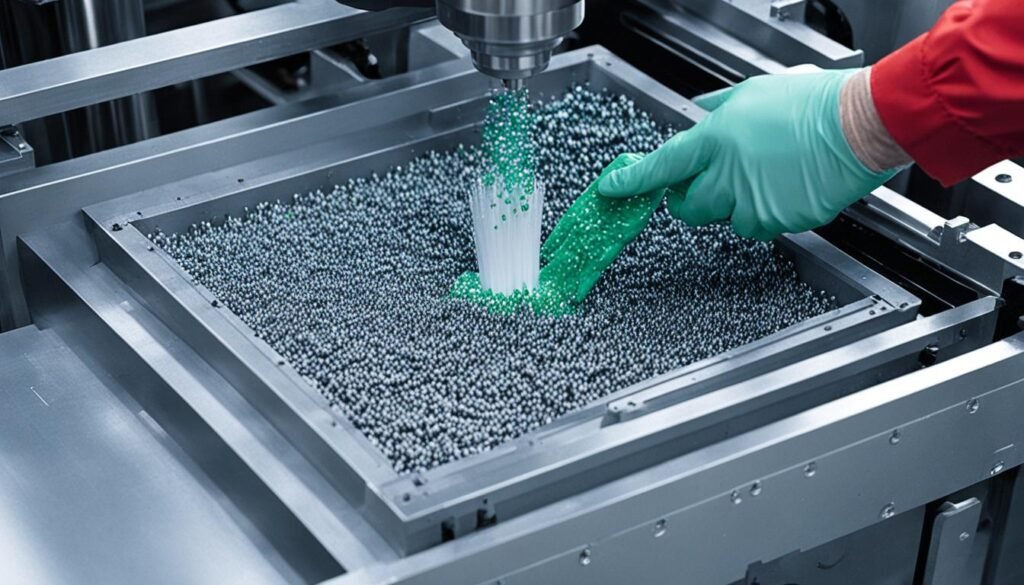
By getting each step of the injection moulding process right, THY Precision makes sure our optical lenses are always top-quality. This process is key to making lots of identical parts quickly and at a good price.
Tooling: The Foundation for Repeatable Injection Molding Optical Lenses Process Step by Step
At the core of the Injection Molding Optical Lenses process is the mold. It’s key for making parts of high quality. Designing and making the perfect mold is tough and important. It affects how well the whole manufacturing process works. THY Precision’s product design team works with tooling experts to make, test, and improve the mold. This ensures it can make the same optical lenses over and over.
The injection moulding tooling is crucial for precision and consistency in making optical lenses on a large scale. Even though it costs a lot upfront, it’s needed for quality and performance.
THY Precision’s mold design process includes prototype development, testing and optimization, and careful attention to details. They work with clients to understand each project’s needs. Then, they create custom tooling solutions.
This teamwork helps THY Precision make injection moulding tooling that consistently produces high-quality optical lenses. It lowers the chance of defects and makes the injection molding process step by step reliable.
“Investing in the right tooling is essential for achieving the level of precision and repeatability required for large-scale optical lens production.”
By focusing on strong, dependable injection moulding tooling, THY Precision lets their clients grow their production safely. They know every lens will be top quality and perform well.
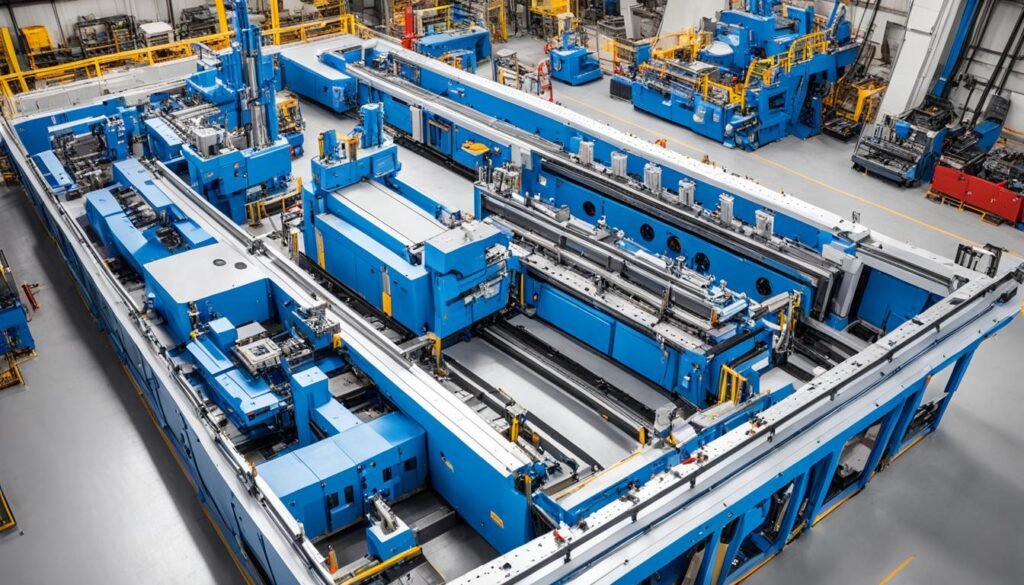
The Injection Molding Optical Lenses step by step
At THY Precision, making high-quality optical lenses is a detailed process. It starts with clamping the mold and ends with ejecting the finished part. Each step is crucial for quality.
Critical Considerations
The injection moulding process has key steps. Each step needs careful attention to keep quality high. These steps include:
- Clamping: Making sure the mold is clamped tight to handle high pressures.
- Melt Preparation: Controlling the plastic’s temperature and viscosity for the right flow.
- Injection: Regulating the plastic injection pressure and speed to fill the mold evenly.
- Cooling: Letting the plastic solidify and the part take shape without warping.
- Ejection: Removing the part from the mold safely without damage.
THY Precision’s experts monitor and adjust these steps for quality. They make sure every lens is consistent and high-quality.
Step | Key Considerations | Optimization Strategies |
---|---|---|
Clamping | Mold stability, pressure tolerance | Precise mold clamping force, mold design |
Melt Preparation | Plastic temperature, viscosity | Accurate temperature control, optimized screw design |
Injection | Injection pressure, flow rate | Precise pressure regulation, flow optimization |
Cooling | Cooling time, part deformation | Efficient cooling system, mold temperature control |
Ejection | Part integrity, cycle time | Gentle ejection mechanism, optimized cycle timing |
THY Precision manages these steps carefully. This ensures they produce high-quality lenses that meet customer needs.
“Attention to detail at every stage of the injection moulding process step by step is essential for producing the precision optical components our customers demand.”
Quality Control and Monitoring
At THY Precision, making sure our quality stays high and catching problems early is key. We use a strong quality control system. This includes checking during production, measuring sizes, and watching the process closely to find and fix any issues.
We really focus on quality control in injection moulding. We know a small mistake can ruin the lens’s quality. Our team watches the process closely. They can spot and fix problems fast, making sure every lens is perfect.
Quality Control Measure | Objective |
---|---|
In-line Inspections | Detect and address any defects or deviations from the specified tolerances during the injection moulding process step by step |
Dimensional Analysis | Ensure the precise dimensions and geometrical accuracy of the molded optical lenses |
Real-time Process Monitoring | Continuously track and analyze key process parameters to identify and mitigate any potential issues in a timely manner |
With these detailed quality control in injection moulding steps, THY Precision makes sure our products are always top-notch. We aim for continuous improvement and customer satisfaction. This is what makes us leaders in making optical lenses.
“At THY Precision, quality is not just a box to check, it’s a way of life. Our relentless pursuit of perfection ensures that each and every lens we produce is a true testament to our commitment to excellence.”
Conclusion
The injection molding process is key for making lots of high-quality optical lenses. At THY Precision, we’ve tackled the challenges of making things the same every time. We use our knowledge of injection molding and always aim to get better.
We manage the whole injection molding process, from making the tools to checking the quality. This has led to great results for our customers in the optical lens industry. Our focus on important process details and strong quality checks helps us make parts that are both affordable and precise.
THY Precision is known as a reliable partner in the optical lens field. This shows we can make injection molded optical lenses that meet strict quality standards. As the need for affordable, large-scale optical lenses grows, we’re ready with our expertise in injection molding. We’re confident our skills will keep helping our customers.