Importance of Aerospace Industry Standards
In the THY Precision injection moulding process step by step for aerospace, following strict standards is key. These standards make sure aircraft parts are safe and reliable. They also help parts work well together and meet important rules.
Federal Aviation Regulations (FAR)
The aerospace industry standards are mainly set by the Federal Aviation Administration (FAA). The FAA has rules called Federal Aviation Regulations (FAR). These rules cover how to design, make, and keep aircraft parts, including those made by the injection moulding process step by step. This makes sure every part is top quality and safe.
International Traffic in Arms Regulations (ITAR)
There’s also the International Traffic in Arms Regulations (ITAR) for the aerospace industry standards. ITAR is from the U.S. Department of State. It controls the sharing of defense items and services, like those made by the injection moulding process step by step. Following ITAR is key for companies to keep sensitive tech safe and stop it from getting into the wrong hands.
“Compliance with industry standards is not just a box to be checked, but a fundamental pillar of the injection moulding process step by step in the aerospace sector.”
By sticking to these tough aerospace industry standards, companies make sure their products are safe, reliable, and easy to track. This helps keep the whole aviation industry strong.
Export Regulations for Aerospace and Defense
Manufacturers in aerospace and defense must follow strict export rules. These rules are set by government bodies. The Export Administration Regulations (EAR) and the Defense Federal Acquisition Regulations (DFAR) are key. They affect the injection moulding process step by step.
The Export Administration Regulations (EAR)
The injection moulding process step by step is under the EAR. This set of rules controls the export and re-export of items. These items can be used for both civilian and military purposes. To follow EAR, manufacturers must make sure their products don’t go to banned countries or for wrong uses.
- The EAR covers many products, like those made through the injection moulding process step by step, that could be used in the military.
- Manufacturers need to classify their products and find the right export control classification number (ECCN) to follow the EAR.
- To export these products, manufacturers must use the right documents and licenses. This can mean getting export licenses or using license exceptions.
The Defense Federal Acquisition Regulations (DFAR)
The injection moulding process step by step is also under the DFAR. This set of rules is for the Department of Defense (DOD) to buy goods and services. If a manufacturer works on government or defense contracts, they must follow DFAR rules.
- DFAR has many requirements, like quality control, testing, and keeping records for products made through the injection moulding process step by step.
- Manufacturers need strong quality systems and detailed records to show they meet DFAR rules.
- If a company doesn’t follow DFAR rules, they could lose government contracts and face other penalties. So, it’s very important to keep up with the latest rules.
Understanding export regulations, export administration regulations, and defense federal acquisition regulations is key for aerospace and defense manufacturers. By knowing these rules well and following them, companies can make sure their products are up to the high standards needed in these industries.
National Institute of Standards and Technology (NIST) Guidelines
THY Precision is a top name in aerospace manufacturing. It follows the strict standards of the National Institute of Standards and Technology (NIST). NIST is a key agency that sets quality, safety, and reliability standards for many industries, including aerospace.
THY Precision sticks to NIST guidelines for its injection molding process. One important guideline is NIST SP 800-53. This standard helps protect federal information systems and organizations. It’s used by government agencies and contractors in aerospace and defense to keep their systems safe.
NIST Guideline | Description | THY Precision’s Compliance |
---|---|---|
NIST SP 800-53 | Provides a catalog of security and privacy controls for federal information systems and organizations, including those involved in the aerospace industry. | THY Precision strictly adheres to the NIST SP 800-53 guidelines to ensure the security and integrity of its injectionmouldingprocessstepbystep operations and data. |
By following NIST guidelines, THY Precision shows it’s serious about making top-quality, secure aerospace parts. This focus on quality gives THY Precision a big edge in the aerospace market.
THY Precision also looks at other NIST standards to make sure its process is consistent and reliable. By using these best practices, THY Precision proves it’s a trusted supplier in aerospace.
AS9100D Certification for the Aerospace Industry
The AS9100 quality management standard is key for companies in the aviation, space, and defense (ASD) sector. It includes those working on the injection moulding process step by step. AS9100D is the latest version, based on ISO 9001 but with extra rules for aerospace.
Additional Requirements for AS9100D
AS9100D has over 100 new rules on top of ISO 9001. These are for the aerospace industry. They cover many areas, like:
- Production control and planning for product realization
- Design and development processes
- Purchasing and control of non-conforming processes
- Product safety and human factors
- Preventative action and counterfeit parts
- Risk management
Getting AS9100D certification shows a company cares about quality and safety in the aerospace industry. It’s vital for THY Precision, a top injection moulding process step by step provider. It makes sure their work and products meet aerospace standards.
“AS9100D certification is a badge of honor for companies in the aerospace industry, showing their commitment to quality, safety, and ongoing improvement.”
With this certification, THY Precision can handle the aerospace industry’s complex rules. They become a reliable partner for companies needing top-notch, injection moulding process step by step solutions.
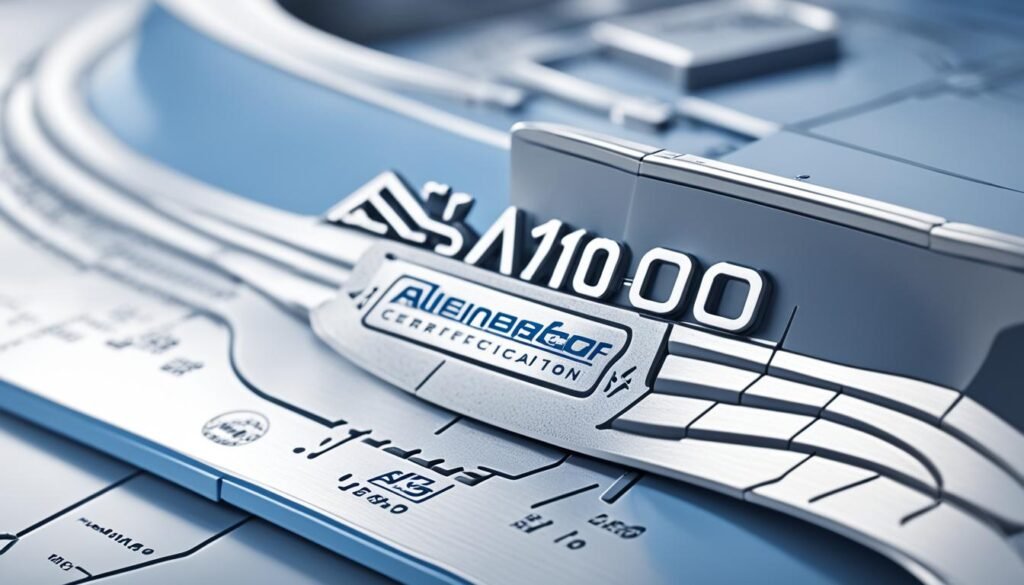
Injection Moulding Process Step by Step
The injection moulding process is key in the aerospace industry. It requires precision and efficiency. At THY Precision, we know how to make sure your aerospace parts are top-notch. Let’s look at the main steps in the injection moulding process.
Material Selection
Choosing the right material is the first step in injection moulding. At THY Precision, we pick the best material for your aerospace project. We think about strength, durability, and heat resistance to make sure your parts work well in tough aerospace conditions.
Wall Thickness
Wall thickness is crucial in injection moulding. The walls of your parts need to be the right thickness for good flow and to avoid warping or uneven cooling. Our experts at THY Precision will help you find the best wall thickness for your aerospace parts. We consider your project’s specific needs.
Transitions and Corners
Transitions and corners affect a part’s strength and performance. At THY Precision, we focus on making these features smooth and strong. This ensures your injection moulded parts can handle aerospace demands.
Draft Angle
The draft angle is vital in injection moulding. It’s the slope on the sides of a part that helps it come out of the mould easily. We calculate the best draft angle for your aerospace parts. We consider the material, wall thickness, and shape for smooth moulding and ejection.
By managing these key steps, THY Precision delivers aerospace components that go beyond industry standards. Our focus on quality, precision, and innovation means your injection moulded parts will work perfectly in tough situations.
Design Considerations for Injection Moulded Parts
Designing parts for the injection moulding process is key. THY Precision knows how important factors like ribs, bosses, tolerances, parting lines, and gates are. These elements help make high-quality, aerospace-grade injection moulded components.
Ribs and Bosses
Ribs and bosses are vital in injection moulded parts. Ribs add strength and increase the part’s load-bearing ability. Bosses support assembly and improve the part’s overall strength. THY Precision adds ribs and bosses carefully to meet aerospace industry standards.
Tolerances
Getting tolerances right is crucial in injection moulding. THY Precision focuses on tight tolerances to make sure parts fit well and work as they should. This is key for aerospace sector needs.
Parting Lines and Gates
Where you put parting lines and gates matters a lot. Parting lines are where the mold halves meet and should be placed to hide them well. Gates are where the material goes in. They must be designed to fill consistently and avoid problems.
Design Consideration | Importance | Impact on Injection Moulding Process |
---|---|---|
Ribs and Bosses | Enhance structural integrity and load-bearing capacity | Requires careful incorporation into the injection moulding process step by step |
Tolerances | Ensure precise fit and function of the final part | Demands strict control and management throughout the injection moulding process step by step |
Parting Lines and Gates | Minimize aesthetic and structural issues | Strategic placement is critical in the injection moulding process step by step |
THY Precision focuses on these design aspects to deliver parts that meet aerospace standards. Their expertise in the injection moulding process and deep aerospace knowledge means clients get parts that look good and work well.
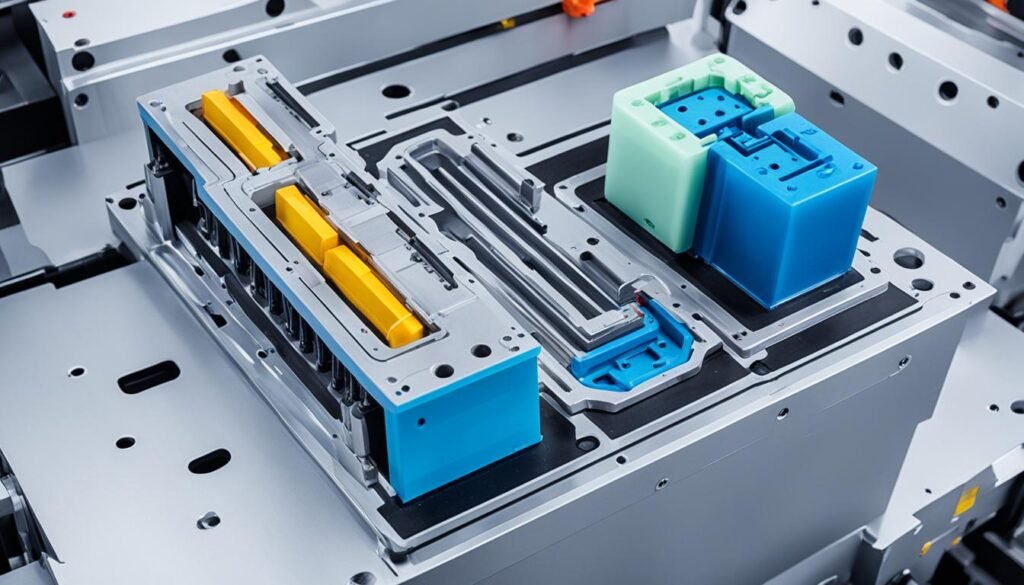
“Attention to detail is paramount in the injection moulding process step by step. At THY Precision, we meticulously design each part to optimize its performance and ensure it meets the stringent requirements of the aerospace industry.”
Moulding Caps and Their Application
In the world of injection moulding, moulding caps are key. They keep the mould safe during the process. This lets the molten material cool and shape into what we want. There are different types of moulding caps, each for a specific use in the process.
Types of Moulding Caps
For a successful injection moulding process, various moulding caps are used. Here are some common ones:
- Standard Caps: These are the most common and work well for many projects.
- Hot Runner Caps: These are for hot runner systems. They keep the material at the right temperature and flow.
- Multi-Cavity Caps: These are needed for complex moulds with many cavities. They help get consistent results.
Applying the Moulding Cap
Putting on the moulding cap right is key. You need to prepare the surface well, place the cap correctly, and press it down just right. If you don’t do this, you might get bad results or even big problems with the final product.
At THY Precision, we know how important moulding caps are. Our experts work hard to make sure your parts are top quality and reliable.
Conclusion
The injection moulding process is key in the aerospace industry. It requires precision, safety, and strict standards. THY Precision knows how to meet these standards, like FAR, ITAR, and NIST guidelines.
This process is complex but vital for aerospace and defense makers. THY Precision excels in choosing the right materials and designing parts. They focus on details like wall thickness and design features. This ensures parts meet high quality and safety standards.
THY Precision supports you in the injection moulding process. Their experts help with AS9100D certification and improving your manufacturing. You can rely on them for quality and compliance in the aerospace industry.